How to Increase the Lifetime of a Motor from Two Weeks to Over a Year: Contaminated Environments
For over 65 years, Dreisilker has been driven to improve our customers’ reliability and increase uptime through problem solving. A common problem we have found for customers is contamination of the motors, leading to premature failure. A unique customer success story relating to failure from contamination involved motors that were failing every 2 weeks. Through talking with the customer and examining their operations, we were able to help them improve the motors’ reliability.
Customer Success Story:
Our customer talked with us about a series of motors that were failing every 2 weeks or less. The motors power large rollers that have water being sprayed over large steel slabs for cooling purposes. The water was negatively affecting these motors and causing failure every two weeks. While the replacement motors were relatively economical, the cost of downtime and the added cost of the labor to uninstall and reinstall was adding up. Our customer asked us if we would be able to come up with a solution to help these motors last 4 to 6 months versus 2 weeks.
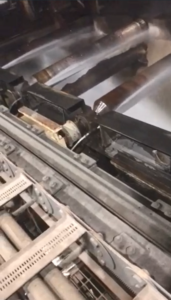
Ultra Seal Application
Our engineering team worked with our customers’ maintenance crew to figure out the best solution for this issue. After reviewing the motor and its application, we determined that it would be best to utilize our Ultra Seal winding technique to fully insulate the motor’s winding and protect it from contamination. The Ultra Seal Winding technique involves us fully impregnating and sealing the coils with a high molecular weight thermoset polymer resin. Below shows a winding before and after the Ultra Seal Winding process.
Left: Ultra Sealed windings. Right: Normal windings.
Crosscut of Ultra Sealed windings.
The customer agreed to try out an Ultra Sealed motor to see how long it would last. The process involved us purchasing a brand new motor, stripping the motor of its windings, winding a new core, and then using our Ultra Seal process. If you are wondering why we would need to strip a brand new motor of its windings, it is because the Ultra Sealed windings do not require standard motor varnish (see our blog on different types of varnishing methods) and it actually acts as the insulator for the windings.
New motor to be Ultra Sealed.
New motor after being Ultra Sealed.
We delivered the new, Ultra Sealed motor to our customer and they put it into production. Two weeks passed by with the motor still running and it exceeded their desired 4-6 month target. The customer recognized the reliability of the new motor and ordered more for the operations and they have been running for over a year.
Some common industrial applications for Ultra Sealed motors include:
• Machine tool CNCs – Servo and Spindle Motors
• Steel Mills: Continuously wet and hot environments that demand reliable 24/7 uptime
• Poultry Processing Facilities
• Irrigation Operations.
• Pulp & Paper Mills
• Mining Operations
• Plastics Injection Molders.
• Petroleum Drilling Operations
• Food Processing
• Foundry Operations
While heat dissipation was not a clear problem with the customer success story above, it is still important for other applications. In addition to protecting the motors from contamination, the Ultra Seal Winding allows for efficient cooling of the motors. The resin used within the process is approximately 40 times more efficient at heat transfer than air. This is useful especially for motors found in extreme temperatures.
If you have motors operating in harsh environments and they are failing prematurely, you may want to consider the Ultra Seal method. Reach out to us today if you have questions regarding the process or would like a quote.