The Basic Steps of Electric Motor Repair
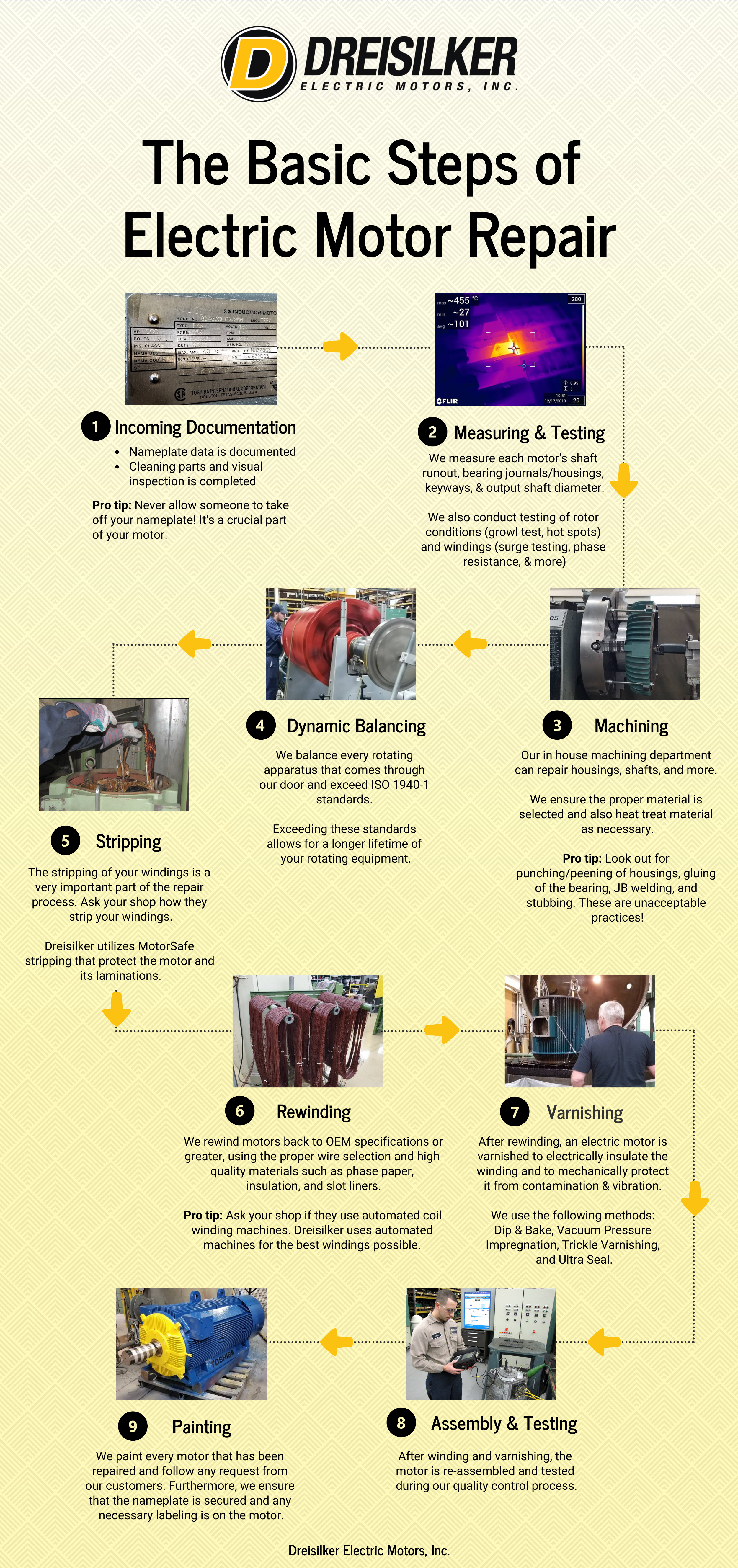
Electric Motor Incoming Documentation:
During electric motor repair, it is vital to document all nameplate information. Never allow someone to take off your nameplate! It’s a crucial part of your motor. We also clean parts and visually inspect the electric motor.
Measuring & Testing during Electric Motor Repair:
When we complete an electric motor refurbishment, we measure the motor’s components such as shaft runout, bearing journals, bearing housings, keyways, output shaft diameter, and more. Furthermore, we also conduct testing of the rotor conditions through a growl test and hot spot tests. At this stage during an electric motor repair, we test the windings through surge testing, phase resistance, insulation resistance megger, Hi-pot (AC destructive, DC non-destructive), and visually insect the electric motor winding.
Machining:
Depending on the condition of the motor, machining is a necessary part of the electric motor repair process. Our in-house machining department works on failed housing, repairing or manufacturing new shafts, and more. For electric motor shaft repair, we can weld and machine shafts, chrome and grind, make a new shaft, and straighten a shaft. We also ensure the proper material is selected and also heat treat material as necessary. Pro Tip: Watch out for some unacceptable practices such as punching/peening of housings, gluing in bearings, JB welding, glue or stubbing).
Dynamic Balancing for Electric Motor Repair:
Dreisilker’s electric motor repair shop follows and exceeds ISO 1940-1 standards for repair on all rotating apparatus. Balancing is an important step in the electric motor repair process, as it greatly impacts the longevity of the motor repair.
Electric Motor Stripping:
The stripping of your windings is a very important part of the electric motor refurbishment process. Ask your shop how they strip your windings. Dreisilker utilizes MotorSafe stripping that protect the motor and its laminations.
Electric Motor Rewinding:
Electric motor rewinding is very detail oriented and can impact the longevity of your electric motor. We rewind motors back to OEM specifications or greater, using the proper wire selection and high quality materials such as phase paper, insulation, and slot liners. Pro tip: Ask your shop if they use automated coil winding machines. Dreisilker uses automated machines for the best windings possible. Check out our blog “The Basics of an Electric Motor Rewind”
Electric Motor Varnishing:
After rewinding, an electric motor is varnished to electrically insulate the winding and to mechanically protect it from contamination & vibration. We use the following methods: Dip & Bake, Vacuum Pressure Impregnation, Trickle Varnishing, and Ultra Seal. Check out our blog on 4 Types of Motor Insulation Methods to learn more.
Assembly & Testing:
After winding and varnishing, the electric motor is re-assembled and tested during our quality control process.
Painting:
The final step of the electric motor repair process is painting. We paint every motor that has been repaired and follow any request from our customers. Furthermore, we ensure that the nameplate is secured and any necessary labeling is on the motor.