There are many factors to review when considering repairing or replacing your electric motor. Some elements include pricing, lead times, condition of the electric motor, past history, and more. Below you will find some general guidelines that we use when working with our customers to determine if they should repair or replace their electric motor.
How critical is your electric motor?
Does the failed electric motor result in your production being ground to a halt, or is it on a machine that you only use occasionally? If your production is down due to this motor failure, your company is losing money. The criticality of your motor to your production line impacts how you will decide to repair or replace your electric motor. This will be discussed further in regards to the cost of repair vs replace, as well as the lead time of the replacement motor.
Do you have a spare on hand? If you have a spare electric motor on hand for your failed motor, it is going to alleviate some of your decision making below because you are not pressed for time. If you do not have a spare, we’ll walk you through how to decide repair or replace when thinking about cost and lead time. We strongly recommend having a spare on hand for critical machines. However, we understand that sometimes it is not financially feasible for some companies to have a spare for their equipment.
Learn more about keeping a spare on hand in our blog post: When to have a Spare Electric Motor
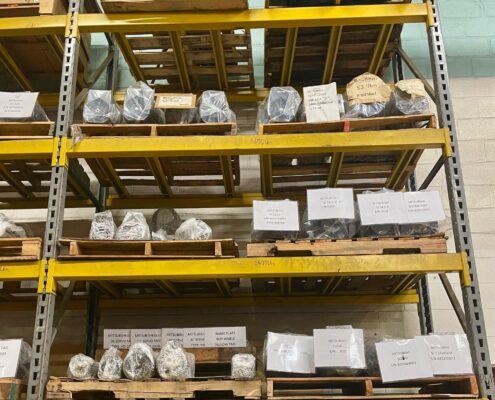
We keep a large stock of spare motors for printing presses and CNC machines so that we can help out our customers in a pinch.
Electric Motor Repair or Replace: Price
Whenever we have an electric motor in our repair shop, we investigate the cost of new for our customers. We always want to provide options so that our customers can make an informed decision on whether to repair or replace. Generally, when the cost of repair is 50% to 80% the cost of new, we recommend a replacement motor. We realize that this is a wide guideline, but there are many factors that go into this decision, such as lead time, energy savings, like for like replacement and etc.
Please keep in mind that one should make sure that the motor replacement option is suitable for your application. Occasionally we witness cost saving methods in the form of finding a cheap replacement from a less reliable manufacturer versus a higher cost – high quality manufacturer. If you choose to go this route, understand that the lifetime and reliability of your motor may be negatively affected and that it can result in higher maintenance costs down the line.
Another factor that can impact the price in this decision is the condition of the motor. If the failed motor requires a simple overhaul, the cost of repair might beat the guideline of 50 to 80% cost of new. However, if a motor requires a complete overhaul (think rewinding, machining work, and etc.) the cost of repair very well may exceed the cost of new.
Does size matter? Once a standard motor is below a certain size, it is more economical to replace than to repair. Generally speaking, any standard AC induction T frame motors at or below 50 to 75 Horse Power (HP) are more economical to replace. Our experienced motor experts will help you with this determination.
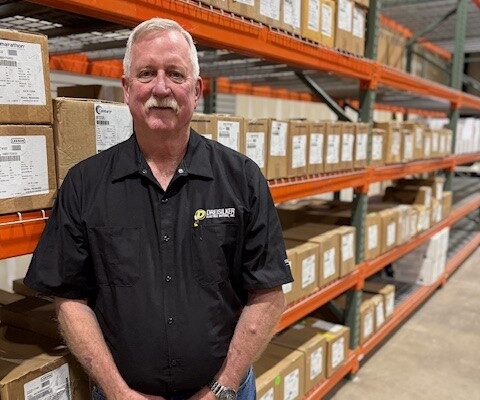
HVAC Motors can typically be more economical to replace than to repair.
Electric Motor Repair or Replace: Lead Time
Finding out the lead time of a replacement motor or repairing your motor is important in your decision making. If there is a replacement motor readily available and its cost is not excessively high compared to repair cost, it’s an easy decision to replace. On the other hand, if the lead time for new is longer than the lead time for a repair, you need to take a step back to evaluate. Here’s an example situation:
Cost of downtime per hour= $1,000/Hour
Standard Hours per week= 40/Week
Cost of New= $10,000, 4 weeks lead time
Cost of Repair= $20,000, 1 week lead time
Cost of new, including lost production would equal: $10,000+($1,000*(40*4))=$170,000
Cost of repair, including lost production would equal: $20,000+($1,000*(40*1))=$60,000
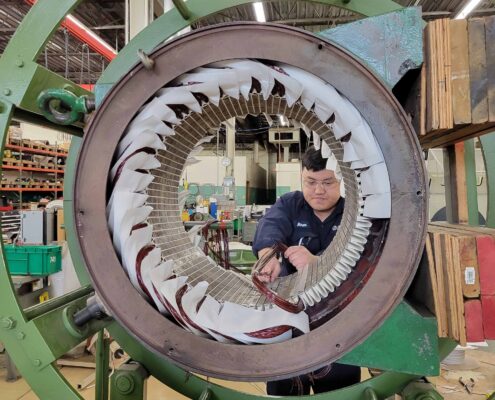
With long lead times for replacement motors, your best option may be to have our experts repair your motor back to new.
Still Unsure On What To Do? Take Our Quick Quiz:
If you’re still weighing the pros and cons, our quick quiz can help guide your decision. Just answer a few questions about your motor’s condition and application — and we’ll recommend whether repair or replacement is the better move.
Electric Motor Repair or Replace: Other Factors
We have gone over two of the most important considerations in your repair vs replace decision: Price and Lead time. While these are the leading factors, some other conditions to think about include energy savings, specifications of a replacement motor, past repair history, and how often this motor has failed in the past.
Energy Savings
Motor manufacturers strive to improve energy efficiencies on their product. If your failed motor is really old, the new motor very well may have better energy efficiencies than your old one. Replacing your motor in this case may lead to energy savings.
Replacement Motor Specifications
While the replacement motor’s nameplate specifications may be the same as your old motor, the size of the actual motor itself may be different (smaller). The smaller size of the new motor may make it difficult for your team to install it in the original application. Double check the dimensions of the motor and its frame with your Dreisilker representative.
In Conclusion
There are many factors that go into deciding whether to repair or replace your electric motor. Our experienced motor experts help many customers every day to make this important decision. We’ll help you figure our pricing and lead time, as well as consider any other factors that may impact your decision. Call us today if you have questions about electric motor repair or replace.